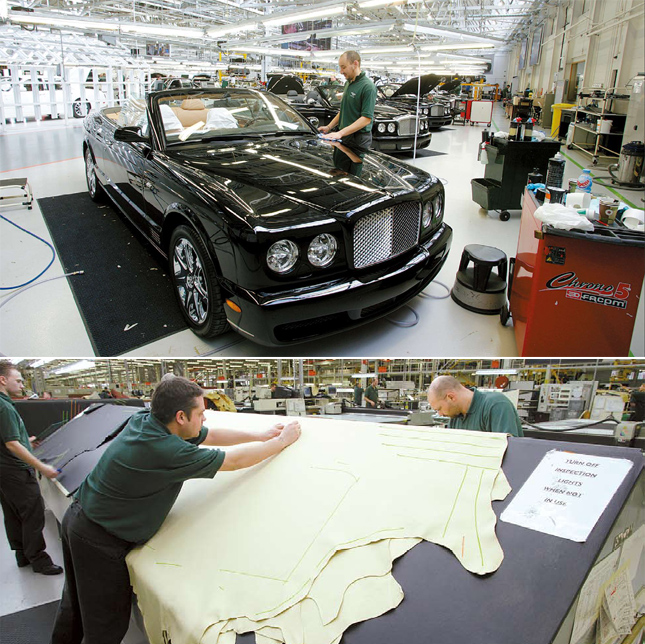
영국 맨체스터시에서 자동차로 40여 분 떨어진 소도시인 크루. 이곳은 영국 최고의 럭셔리 카 업체인 벤틀리 공장이 위치해 ‘벤틀리 타운’으로 불린다. 한국 언론에는 처음 공개하는 공장이다. 영국 왕실 전용차를 만드는 회사다.
英 왕실 전용차 만드는 벤틀리 공장 국내 언론에 첫 공개

올해로 공장 건립 60년을 맞은 크루 공장의 작업자 4000명은 모두 영국인이다. 이른바 ‘브리티시 장인정신’이 이들의 손에서 나온다. 근로자의 평균 나이는 40세로 전원 정규직이다. 하루 8시간씩 2교대로 일하며 한 주에 36시간 근무한다. 여성 근로자 비율은 30% 정도로 다른 자동차 공장에 비해 많다. 이유는 수작업이 많아서다. 가죽 시트 바느질 작업이나 내장재 마무리는 주로 이들이 한다.
작업자의 90% 이상은 크루에 살면서 대를 이어 일한 장인들이다. 3대째 일하는 작업자도 5% 정도 된다.
올해부터 모든 벤틀리는 크루 공장에서만 생산한다. 지난해에는 주문이 넘쳐 전체 물량의 10%를 독일 드레스덴 폴크스바겐 공장에서도 생산했다. 하지만 영국 장인정신을 지키기 위해 올해부터는 이곳에서만 생산한다.
로빈 페이지 수석 디자이너는 “자동차 내장재로 플라스틱은 일절 쓰지 않는다”며 “영국의 우아함을 지키기 위해 가죽ㆍ원목ㆍ메탈(크롬)로만 실내 장식을 한다”고 설명한다.
벤틀리는 2003년 이후 급성장했다. 1990년대 중반 폴크스바겐 그룹 산하로 인수됐다. 2000년에 1700대를 생산했지만 지난해에는 9600대로 역대 최고치를 기록했다.
올해 목표는 1만 대다. 수요가 더 늘어도 1만 대 이상은 생산하지 않을 방침이다. 주문한 뒤 인도까지는 통상 3∼6개월 정도 걸린다.
제임스 바클리 아시아 마케팅 담당 매니저는 “워낙 고가인 데다 수제품이기 때문에 주문이 늘어나도 생산량을 확대하기에는 한계가 있다”며 “89년 역사 동안 주인이 여러 번 바뀐 아픈 과거가 있어 공장 증설보다는 연간 1만 대를 꾸준히 파는 게 목표”라고 말했다.
이곳에서 생산하는 벤틀리의 80%는 2억∼3억원 하는 콘티넨털GT와 플라잉 스퍼 세단이다. 이들 차량은 플랫폼(엔진과 차체)이 같다. 콘티넨털GT는 세계에서 가장 빠른 쿠페(2인승의 세단형 승용차)다. 550마력을 내는 6ℓW12(V6 엔진 두 개를 붙여놓은 형태) 엔진을 얹고 시속 300㎞ 이상 달릴 수 있다. 벤틀리의 부활을 확인해준 차다. 미국에서 전체 판매량의 50%가 팔린다. 한국계 미식축구 선수인 하인스 워드가 타는 차로도 유명하다.
뒷좌석이 넉넉한 플라잉 스퍼는 콘티넨털GT에 사용하는 엔진을 달았다. 시동을 걸면 벤틀리의 유전자가 느껴진다. 스포츠카의 전통을 이어받아 으르렁거리는 엔진 배기음이 뒷좌석에 살짝 들려온다.
조립라인은 유심히 보지 않으면 마치 정지된 것과 같다. 약 200m의 ‘U’자형 조립라인에선 평균 17∼20분마다 차가 한 대씩 나오기 때문에 1분에 5∼8m 정도 움직인다. 현대차는 보통 1분에 한 대, 도요타는 50초 만에 한 대를 생산한다. 대중차와 수작업차가 다른 게 이런 것이다.
안내를 맡은 마이클 가넷은 30년간 작업라인에서 일하다 3년 전부터 공장 안내를 맡고 있다. 그는 “모든 조립공정은 앞유리 접합을 빼고는 모두 손으로 작업한다”며 “볼트를 죌 때 로봇의 힘을 빌리더라도 정확히 죄어졌는지는 반드시 사람이 확인한다”고 설명한다.
차체와 파워트레인(엔진ㆍ변속기)을 접합하는 공정 앞에 다다랐다. 로봇이 무거운 차체를 서서히 내리면 네 명의 작업자가 15개의 거대한 볼트를 직접 손으로 조여 조립한다. 이 공정에만 5분이 걸린다.
조립라인 옆에 마련된 또 다른 공정에선 40대 여성들이 최고급 가죽으로 만든 시트에 다시 한번 바느질로 수를 놓는다. 가죽을 꿰맨 자국 위에 검은 실로 고급스러움을 주기 위해 다시 한번 X자 형태의 수를 놓는다. 이런 처리를 하는 옵션 가격은 2500파운드(약 400만원)다. 한 사람이 하루에 보통 3∼5대 분을 만든다. 시트 등 실내 장식에는 한 대당 12∼20마리의 소가죽이 사용되는데 모두 손으로 바느질을 한다.
가넷은 “20년간 바느질만 해온 작업자들이 100여 명”이라며 “실내장식도 모두 원목을 써 숙련 기술자가 손 가공하는 게 벤틀리가 다른 고급차와 구별되는 요소”라고 설명한다.
다음은 실내 인테리어 공정이다. 장인정신의 혼이 깃든 곳으로 고급 가구회사에 온 느낌이다. 대패와 끌을 든 50여 명의 장인들이 실내장식에 쓸 원목에 베니어를 붙인다. 숙련 작업자가 되는 데 적어도 10년간은 보조로 일해야 한다.
이런 벤틀리에도 2005년부터 도요타생산방식으로 유명한 ‘가이젠(改善)’ 바람이 불고 있다. 비용을 절감하고 작업자 충원이나 공장 증설 없이 생산성을 높여 증가하는 주문에 대처하기 위해서다. 작업자들에게 생산성을 높일 수 있는 공정 제안을 받아 개선을 했다. 공장 곳곳에 ‘가이젠’을 써 붙여놓고 근로자들을 독려한다. 이 덕분에 지난해 생산성이 10% 정도 높아졌다고 한다.
특히 하나의 작업라인에서 여러 차종을 만드는 혼류 생산에 열심이다. 재고를 줄이고 탄력적으로 수요에 대처하기 위해서다. 이런 도요타생산방식 접목 덕분에 콘티넨털GTㆍ플라잉 스퍼ㆍ최고급 세단 아나즈가 하나의 조립라인에서 생산된다.
스튜어트 매컬러프 판매총괄 부사장은 “벤틀리가 1만 대만 생산하는 것은 소유한 사람들이 희소성을 느낄 수 있는 한계수치”라며 “경기 침체로 재고가 쌓여 망했던 역사가 여러 번 있어 생산 공정은 절대 늘리지 않을 것”이라고 말한다.
내장 컬러 개발실에선 한국인 심경희 연구원이 반갑게 맞는다. 대우차 영국법인에서 일하다 회사가 망해 랜드로버를 거쳐 5년 전 벤틀리에 입사했다. 심 연구원은 “고객이 직접 공장을 방문해 상담실에서 40여 가지 컬러를 보면서 대여섯 개를 골라 내장을 꾸민다”며 “최근에는 파스텔톤 색을 찾는 고객이 늘고 있다”고 설명했다. 지난달에는 포뮬러1(F1) 드라이버로 유명한 마이클 슈마허가 헬기를 타고 이곳을 찾아 직접 색을 선택했다고 했다.
그는 또 “2, 3년 전부터 벤틀리에도 비용 절감 바람이 강하게 불고 있다”며 “극소수만을 위해 제작하는 수작업의 전통은 지키지만, 수익을 내고 고용을 유지하기 위해 비용 절감과 수익성 개선에도 열심”이라고 말한다.
다음은 공장 한 곳 비밀스러운 별도의 작업실이다. 유럽의 왕족이나 중동 부호들이 타는 특수 제작차나 방탄차를 만드는 곳이다. 일반 작업자들의 출입을 제한한다. 5억원대 최고급 세단 ‘아나즈’를 기반으로 만든 방탄차는 30억원을 호가한다.
차체 크기나 실내 디자인은 고객의 요구대로 제작해준다. 방탄유리를 끼우는 공정에는 총알이 박혀 있는 실험용 유리가 전시돼 있다. AK 소총으로 사격한 뒤 제대로 방탄이 된 것을 고객에게 확인시켜 주기 위해서다.
다음달 중동의 한 부호에게 인도될 30억원짜리 아나즈 방탄차의 길이는 무려 7m가 넘는다. 방탄유리는 물론 수류탄이 터져도 시속 80㎞로 달릴 수 있는 차체를 갖추고 있으며, 실내에는 와인 바까지 갖추고 있다. 특급 호텔의 스위트룸을 보는 듯하다. 이 차에만 30마리의 소가죽이 사용됐다.
벤틀리는 분명 자동차 역사에 한 획을 긋는 업체다. 수공을 고집하면서 소량 생산을 통해 브랜드 명성을 지켜왔다. 하지만 급변하는 자동차 산업의 치열한 경쟁 속에 수작업과 생산성 향상이라는 두 마리 토끼 가운데 고심하는 흔적을 엿볼 수 있었다.